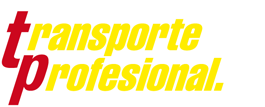
Llega el turno de la informática, de la simulación, de la realidad virtual, hasta alcanzar extremos insospechados.Hemos viajado hasta el Centro de Diseño y Desarrollo que Renault posee en Saint Priest, cerca de Lyon (Francia), con el mejor guía posible, Thierry Hours, vicepresidente de Renault Trucks y máximo responsable del desarrollo de la nueva gama de la marca, quien nos ha desvelado uno de los secretos mejor guardados: “cómo se hizo”.
La simulación informática
Entramos en una sala repleta de pantallas y ordenadores, con una plataforma donde una persona –que simula ser un conductor- está sentada en un asiento real de camión, frente a un volante con su columna de dirección. Un ingeniero le coloca un casco y unos guantes dotados de cables y sensores: acabamos de entrar en la realidad virtual; en este caso, en el interior de la cabina de un camión que de hecho no existe. Sin embargo, a través de unas pantallas “vemos” todo lo que hace el conductor. Éste dirige sus brazos, manos y dedos, alcanzando el volante, los controles y todos los compartimentos de la cabina. Se trata de saber cuál es la mejor posición de todos los elementos, aunque todavía no están configurados en la realidad, en función de la talla y la corpulencia del individuo, conocer, en suma cómo hacerlos más ergonómicos, más confortables y cómo mejorar la vida a bordo.
Como nos explica Thierry Hours, “esta plataforma virtual nos ha permitido, desde el inicio del proyecto y antes de fabricar cualquier prototipo, definir la ubicación de los mandos en el tablero de instrumentos, o los espacios, además del tamaño del parabrisas o incluso la posición de los retrovisores”. Esta realidad virtual, esta simulación perfecta, permite pasar de la idea a la fase de preserie de los vehículos.
Cinema en tres dimensiones
Es simplemente espectacular. Entramos en una sala de proyección para “ver”, como en una película en 3D, la proyección de imágenes, a escala real, del vehículo que se pretende diseñar y construir. Aquí la herramienta informática proyecta la simulación de diversas impresiones, en cuanto al aspecto e incluso la calidad del vehículo, con cambios de color y ajustes diversos entre sus diferentes piezas. Esto es lo que se mostró a los altos ejecutivos de la marca, antes de pasar a la fase real. Aquí se decidió el aspecto final que tendrían las unidades de las nuevas gamas. Los deflectores de los faros, por ejemplo, fueron objeto de múltiples cambios, antes de la aprobación final.
Modelar en 3D
La técnica se llama estereolitografía, y parece cosa de magia. Se trata de modelar piezas en tres dimensiones, partiendo de archivos digitales, la misma técnica que se utiliza en Fórmula 1. Las piezas, de diversos tamaños y formas muy complicadas, se crean –con la colaboración del láser y sin ningún tipo de herramientas- en un baño de resina, capa por capa hasta la terminación definitiva del prototipo, que se solidifica al contacto con el aire. Gracias a este sistema, “es posible –indica Hours- ensayar y modificar rápidamente los instrumentos del tablero de mando, por ejemplo y fabricar las herramientas industriales sólo cuando estamos eguros de que el resultado responde a nuestras exigencias”.
La cámara anecoica
En realidad es un cubo metálico perfecto, una cámara electromagnética, una “caja de Faraday”, cuyo objetivo es verificar que los vehículos estén a salvo de cualquier perturbación electromagnética y medir las emisiones magnéticas que puedan producir ellos mismos. Impresiona estar dentro, con sus paredes cubiertas de conos de poliuretano rellenos de carbono. Sus dimensiones permiten albergar casi cualquier vehículo industrial (se han probado 19 configuraciones, además de 180 conjuntos eléctricos y electromecánicos). Nunca nos paramos a pensarlo, pero en la vida real cualquier vehículo está sometido a la influencia de ondas o campos electromagnéticos de todo tipo, como peajes, líneas de alta tensión, antenas de TV y radio…, que pueden dejar al camión sin control. Esta “caja” ayuda a conocer y aislar estas interferencias, mediante un complejo proceso de pruebas, hasta hacerlos inmunes, sometiéndolos a tensiones tres veces superiores a la normativa europea: desde 100 kilohertzios y hasta 3 gigahertzios. Debe tener en cuenta que hasta un simple móvil, colocado frente al cuadro de mandos, podría desbaratar las funciones de éste. Las pruebas se hacen con el primer vehículo y continúan en la vida real del mismo y en las futuras evoluciones de la gama.
Las pruebas más exhaustivas
El centro de experimentación y desarrollo de motores es también espectacular. Para las nuevas gamas se han testado 600 motores en banco y en carretera. El centro cuenta con 25 bancos, con funciones específicas, desde probar el arranque con temperaturas de -40 a + 60 grados centígrados, o medir la eficiencia, el ahorro de consumo y la fiabilidad. Nada menos que 300.000 horas de pruebas han sufrido los bloques Euro 6 de 11 y 13 litros. Se busca la fiabilidad hasta 2 millones de kms. ó 15 años de vida. El 11 litros se ha desarrollado en Lyon y el 13 litros en Gotemburgo, en las instalaciones de Volvo, aunque las pruebas de ambos se han hecho en Lyon, porque los test de potencia son diferentes, así como las potencias de cada una de las marcas. Laponia y Sierra Nevada son algunos de los lugares donde se han realizado las pruebas de campo. La reducción del consumo ha sido uno de los puntos vitales. Se pueden simular diferentes tipos de conducción durante el tiempo que se desee, con distintos tipos de recorrido, etc., para que la eficiencia de la conducción sea exacta, de forma que se puedan hacer cambios en los parámetros más adecuados. Esto es más exacto aún que las pruebas en carretera, porque se repiten las condiciones, sin el concurso de la climatología o el tráfico.
Por supuesto, todos los elementos del vehículo (chasis, cadena cinemática, circuitos eléctricos y neumáticos, cabina, etc.), han pasado duros controles, con ensayos repetidos miles de veces. En carretera, más de 32 prestaciones diferentes son medidas para asegurar la calidad, la eficiencia y la fiabilidad del producto final.